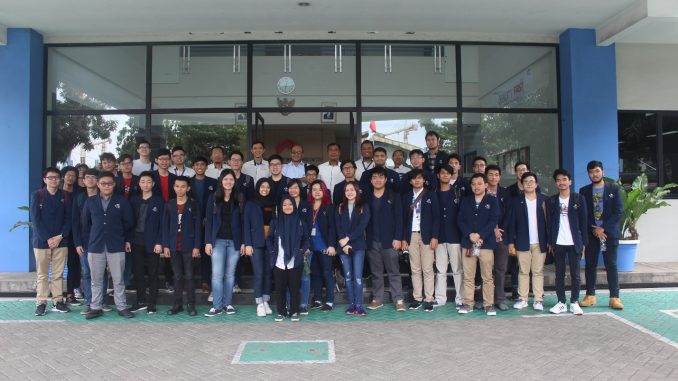
(By: Raihan Khafidz MTE 2016)
As future leaders of the industry of Indonesia, we, young engineering students of IULI, could learn a thing or two from looking at one of the top companies when it comes to mass producing car parts and stamping. IPPI, Inti Pantja Press Industry, is a company within the ASTRA motor 3 group and mainly in charge of press manufacturing for motor vehicles, components, and other related jobs for companies like Isuzu Astra Indonesia, Astra Daihatsu Motor, Nissan motor Indonesia, Astra Nissan Diesel, and Honda Prospect Motor. We had the fortunate chance to take a guided tour of the factory facilities by some of the company’s higher ups, who have been in the industry for more than two decades.
We arrived on site at 9 am sharp, and by the signs of cautions everywhere and the designated pedestrian walkway painted on the roads, anyone could tell that they run a strict and mindful operation. Before we got to walk around and tour the factory site, the president, director and some of the upper management started our day by telling us the vision and mission and a little bit of the history of the company. IPPI has been around for around 2 decades and has grown to be one of the titans in press steel manufacturing with a staff of around 500 people that works all year round. The assured us that they will uphold the quality of their products and ensure competitive prices. After some preliminary questions about the company, we were set with some protective gear and set off to look around the site and see what we can look forward when dive into this industry.
The first significant portion that we got a close look at is the training areas that are scattered throughout the different segments of the site. As most of the labor workforce comes from high school or SMK graduates, they would need to be trained to operate the different machinery and how to inspect the different work pieces for any imperfections or anything that might cause difficulties or damages along the line of machining and storage.
We were then split into two groups, one following the process in order while the other followed in reverse order. Typically, one would not be able to take pictures within the factory but we were given the opportunity to take as many pictures as needed because they said that they do not fear if it’s only university students as it would only propel us to be more inspired and motived to dive deeper into the industry and improve upon it.
The first machine we got to witness working was this large pressing machine that towered over everything as it is almost two stories tall. Its purpose is to press metal sheets and cut them into the shape of the mold of a specified car part called a “Dice”. The Dice used can be exchanged depending on the work needed to be done. These machines are semi-automated, meaning that they can do most of the work by themselves but still needs human operators for certain functions like loading the sheets at the beginning of the process, exchanging the dice for another, and inspecting the results at the tail end of the process.
The finished stamped sheet is then taken to the inspection area in order to find any missed details or imperfections. The stamped pieces are put up against a wooden sample of what a piece should be and if it does not pass the inspection then the batch it came from needs to be investigated. The finished stamped pieces are taken to the spot wielding for further detailing. The wielding is done by multiple people with the use of hanging wielding torches that are controlled using a PLC system.
After all the processes are done with, the data is logged and the pieces are placed in storage on the other side of the factory, waiting to be shipped out. Everything that happened within the day is logged to the minutes and any deviation from the plan needs to be investigated as to why.
After the tour, we were guided back to the starting to room to ask some follow up question about the inner workings of the company or specific processes that were unclear. Most of the people on site were very welcoming and helpful when we wanted to ask questions. The entire experience was a joy to go through and IPPI has clearly built a professional and intelligent working environment and work culture around itself. Thank you IPPI for welcoming us and may our relations continue to grow and prosper.